
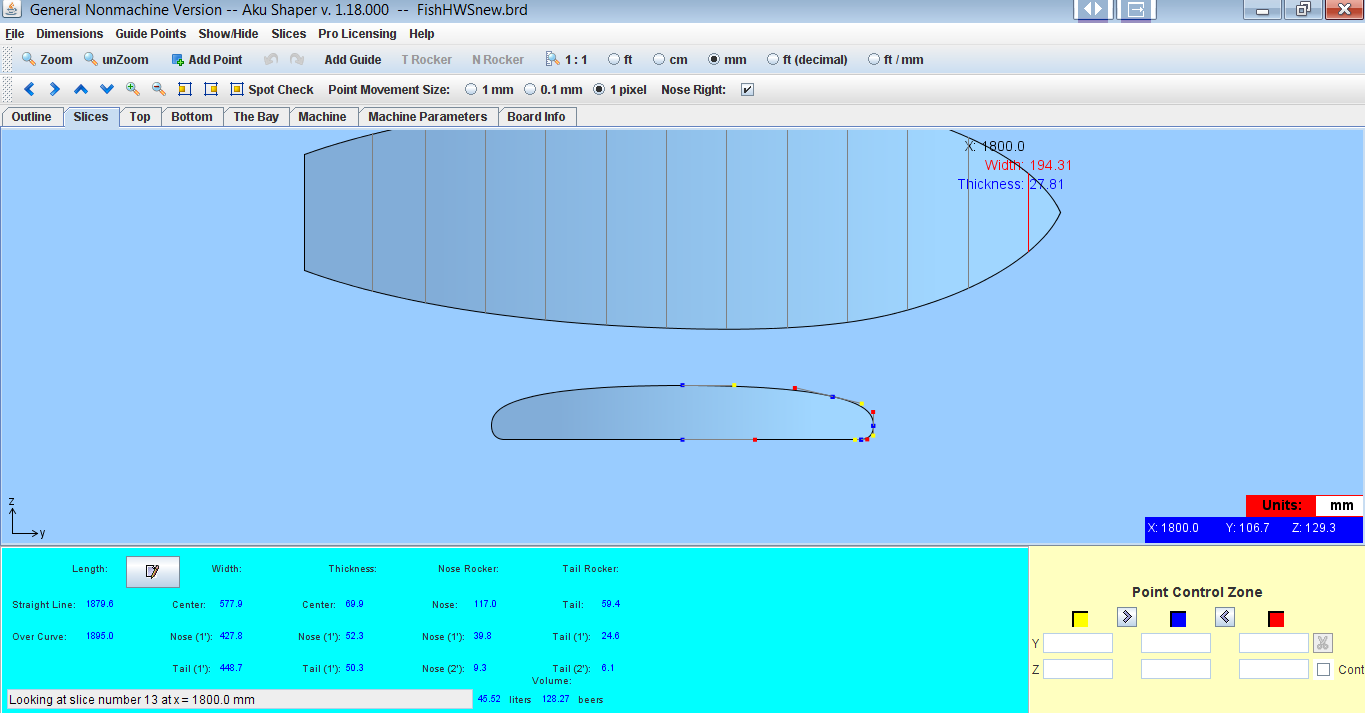
Top, cut by computer, and bottom, finished by hand I can’t justify that money for something that’s not yet going to save me time.” “Right now,” says Dale, “the set up just ties up the machine too much, and I can do it by hand in half the time. “The set up time is what slows it,” explains Dale.Īs the router is a different cutting head to what’s used on the rest of the board, it takes time to switch out and set it up, and that time has to be billed for. The issue at this point is that the bulk of Dale’s orders are customs, with each board slightly different to the one before and after. In fact, they can do what I want, the only problem right now is the time.” “We’re just trying different things out,” continues Dale, “We’re getting close. “The program is better,” says Dale, who’s working with Shape3D now, “and I really like what the Elite Cutting crew are doing.” He was, however, open-minded about the possibilities.įast forward five years, and Dale has again been playing with a router on a machine cutter, this time at Elite Cutting in Tweed Heads. Yet the channels he usually shapes - think deep, sharp, and long - lay beyond the router’s capabilities. “I can see how the tool can work,” said Dale, suggesting they’d be ideal for shallow tail channels. Every popular design feature can be sculpted with ease, except for one - channels.įive years ago, upon the release of a router that could cut inlays for carbon wraps and fin systems, and also approximate a channel bottom, Swellnet spoke to three leading channel shapers to get their opinion, one of whom was Dale Wilson from Byrning Spears.ĭale was curious about the technology but still hesitant about its application. These days machine cutters can produce an array of curves and contours out of a crude foam blank.
